Ensure the robustness of your products with HALT & HASS testing
The purpose of HALT and HASS testing is to build robustness into your products from the earliest stages in their development cycle.
These tests allow you to strongly reduce, or even eliminate, the teething problems experienced by new products.
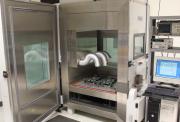
HALT tests generally take between 3 and 5 days, which is nothing compared with the weeks and months required to secure design approval.
The results are clear to see: your products hit the market sooner, are more reliable and generate less work for your after-sale service team.
The major advantages of HALT testing are as follows:
- Greater customer satisfaction,
- Increased quality/reliability,
- Rapid detection of the weak points in your designs,
- Reduced research & development costs,
- Shorter development times,
- Reduced time-to-market delay,
- Understanding and improving the design margins of your products,
- Detecting and correcting faults before products go on sale (or before they are submitted for certification),
- Fewer after-sale repairs required during the guarantee period,
- ...
The HALT methodology yields optimal results when applied during the product design phase, but can also be called upon to deliver targeted benefits at other times:
- Solving compliance issues detected during the certification process,
- Reproducing defects reported by clients.
HASS testing builds on these advantages by correcting defects arising from production lines (modification of fabrication processes, new component suppliers etc.).
Covering the whole life cycle of a product series, HALT & HASS tests allow you to take action at all three key phases of the bathtub curve, representing the evolution of the failure rate over time.
HALT and HASS tests
HALT is an acronym for Highly Accelerated Life Testing, a term used to cover a series of thermal and mechanical tests conducted on new products during the design phase.
Our applied methodology makes it possible to detect design defects and weaknesses in electronic systems and sub-components. If left uncorrected, these defects could emerge during environmental testing (where such tests are conducted) or once the product hits the market.
HASS is an acronym for Highly Accelerated Stress Screen, an advanced form of debugging. During the production process, all or some of your electronic components are subjected to thermal and mechanical constraints of varying severity. The HASS testing methodology brings to light defects which can be attributed to the fabrication process.
HALT and HASS test methodology
You can find more information on our dedicated HALT & HASS page
Our HALT & HASS reliability workshop
Equipped with a 1.14m3 HALT & HASS test chamber.
- Volume: 1140 dm3
- Temperature: -100 à +200 °C
- Rapid temperature variation: up to 60°C/min
- Vibrations:
- random and omni-axial
- frequency range 10 to 10000 Hz
- maximum acceleration: 60 gRMS
Meeting the very latest reliability requirements.
At the design stage, maximise the robustness of your products by exploring the limits of their functionality and structural integrity.
In the manufacturing phase, eliminate underlying faults and optimise your fabrication processes and supply chains.