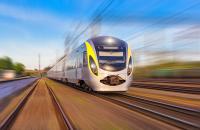
Tests related to engines (combustion, micro-hybrid, hybrid, electric) of complete vehicles or their components (powertrain or other component) require different test bench technologies (inertia test bench, brake test bench, dynamic test bench) in different versions: roller test benches, PWT and e-PWT benches, engine test benches, engine component test benches, characterization benches...
A test bench is a set of equipment installed in a room generally tempered and ventilated. It can be very simple in the case of elementary engine function tests, or very complex in the case of simulation of real operation of a PWT or a complete vehicle.
Our engineering department has a strong expertise in this field having already designed many benches for our internal needs (powertrain test bench, e-motor test bench, ElectroMagnetic Compatibility test bench, etc.) and to cover the needs of our customers.
Our services on test benches can have several objectives. It can be about tests :
The test benches for testing vehicles and their various components (complete powertrain or sub-assemblies) are almost as numerous as the parameters that need to be optimized for more efficient mobility.
Climatic Sector | |||
High capacity climatic roller test bench (Air -30 to +60°C) | Dynamic | 180 kW | - |
High capacity climatic roller test bench (Air -30 to +55°C) | Dynamic | 160 kW | - |
Climatic engine test bench (Air -30 to +50°C / fluides on consultation) | Dynamic | 230 kW | 1000 Nm |
Climatic engine test bench (Air -30 to +50°C / fluids on consultation) | Dynamic | 220 kW | 1000 Nm |
Mechanical and energy sector | |||
Engine test bench | Dynamic | 144 kW | 460 Nm |
2 Engine test benches | Dynamic | 220 kW | 460 Nm |
Engine test bench | Dynamic | 230 kW | 1000 Nm |
Engine test bench | Dynamic | 300 kW | 500 Nm |
Engine test bench | Stationary | 130 kW | 270 Nm |
Engine test bench | Stationary | 230 kW | 750 Nm |
3 Engine test benches | Stationary | 300 kW | 500 Nm |
2 Engine test benches | Stationary | 294 kW | 900 Nm |
Engine test bench | Stationary | 300 kW | 900 Nm |
Engine test bench | Stationary | 590 kW | 4000 Nm |
PWT / e-PWT test bench (Max. couple from 2000 Nm @1000 rpm to 640 Nm @3000 rpm) - More | Dynamic | 2x200 kW | 2000 Nm |
Multi-purpose test bench aeronautics, propeller engine | Stationary | - | 1600 Nm |
Secteur émission | |||
Large capacity climatic chassis dynamometer (Air -30 to +60°C) - More | Dynamic | 186 kW | - |
Secteur composants | |||
Electric test bench - 2 machines (48V) (Max. couple from 70 Nm @12000 rpm to 53 Nm @18000 rpm / 60 Nm @11000 rpm to 28 Nm @24000 rpm) - More | High dynamic | 100 kW / 70 kW | 70 Nm / 60 Nm |
e-PWT or transmission (Max. couple from2238 Nm @1500 rpm to 1000 Nm @2800 tr/min) - More | Dynamic | 2x369 kW | 2238 Nm |
Electric test bench with climatic option (Max. couple from 510 Nm - Max. speed of 21000 rpm) - More | High dynamic | 270 kW | 570 Nm |
ElectroMagnetic Characterization of Electric Motor (Max. couple of 510 Nm - Max. speed of 21000 rpm) | High dynamic | 270 kW | 510 Nm |
Battery test benches - More | - | - | - |
Battery abuse test bench (deformation, crushing, impalement) | - | - | - |
Fuel pump characterization bench | - | - | - |
Water pump characterization bench | - | - | - |
Attitude test bench | - | - | - |
Altitude simulation test bench | - | - | - |
Engine architecture | |
Combustion analysis (combustion characterization, knocking robustness, combustion efficiency...; engine internal aerodynamic development, combustion model recalibration) | Stationary bench |
De-oiling development (oiler geometry development and efficiency characterization) | Stationary bench |
Production conformity (running-in, full load curves) | Stationary bench |
Vibration characterization (vibration measurements on engine components, e.g. alternator, to identify vibration levels and frequencies; operational deformation on powertrain; operational deformation of exhaust line; transfer function on vehicle) | Stationary bench |
Thermal characterization (thermal balance: measurement of the energy introduced by the fuel and of all useful and lost energy; thermo management: optimization of the heating of an engine with control of one or more thermostats; engine thermometry or engine function) | Stationary bench |
Special fuels tests (knocking calibration; dedicated export engine calibration; robustness of pollution control devices for special fuels; accelerated aging of pollution control devices) | Stationary bench |
Exhaust Gas Recirculation (EGR) system development (Implementation and tests on gasoline or diesel EGR systems, super-cooled or not) | Stationary bench |
Friction losses measurements (Average friction pressure in combustion: engine friction measurement in combustion with influence of load, crankshaft misalignment...; Average friction pressure in driven: complete engine friction measurement or station to station; Average friction pressure in thermal transient: friction losses measurements in driven station to station or in fire on the stabilized points of a cycle, in thermal transient) |
Mixed bench (braking & driving) |
Characterization of functions in steady state (characterization of distribution drives, measurements of instantaneous cuts of distribution drives...) | Stationary bench |
Characterization of functions in transient regime (response time and turbo pumping, lubrication circuit in high transient ... ; Development of turbocharger, characterization of e-turbo, measurement of oil consumption of a turbo and its permeability) | Dynamic bench |
Characterization of the lubrication circuit (permeability of the oil circuit, measurement of pressures at different points) | Mixed bench (braking & driving) |
Characterization of the oil consumption | Mixed bench (braking & driving) |
Cangine calibration - Gasoline & Diesel | |
Calibration of functions (strategy of response to throttle off: injector recalibration, turbo maintenance...; pre-calibration of approval before driving) | Dynamic bench |
Calibration de fonctions (bruit de combustion sur montée en température ; calibration injection avec validation cartographie d’injecteurs ; dépollution ; MAP agrément / bruit / fiabilité ; MAP boucle d’air pour une adaptation turbo ; MAP EGR ; MAP FAP : régénération du filtre à particule ; MAP performance pleine charge et dynamique ; MAP structure coupe ; passage à un nouveau carburant ; Courbes de sensibilité : contre-pression, température après échangeur…) Calibration of functions (combustion noise on temperature rise; injection calibration with injector mapping validation; pollution control; development of pleasure / noise / reliability; development of air loop for turbo adaptation; development of EGR; development of particle filter regeneration; development of full load and dynamic performance; development of cutting structure; changeover to a new fuel; sensitivity curves: back pressure, temperature after exchanger, etc.) |
Stationary bench |
Calibration of functions (calibration of the engine friction torque: validation of friction mapping; positioning of effective specific consumption / pollution control) | Mixed bench (braking & driving) |
Engine calibration (measurement of parameters: consumption, pollution, average friction pressure... on driving cycles) | Dynamic bench |
Arngine achitecture | |
Endurance and reliability of the complete engine (validation of the engine equipped with the Stop & Start function; simulation of driving cycle according to the profile provided: vehicle and road cycle data, speed and gear engaged according to time, etc.) | Dynamic bench |
Endurance and reliability of the complete engine (thermal shocks; road cycle, urban cycle...; measurement of wear evolution; gumming; seizing; lubrication; continuous full load; idle; overspeed) | Stationary bench |
Endurance and reliability on components (tests of sensitive components in transitory: turbos, particle filters...) | Dynamic bench |
Endurance and reliability on components (alternator; balance shaft; exhaust manifold; turbo corrosion; timing belts; Exhaust Gas Recirculation fouling; injector fouling; catalyst aging; oil aging; coolant aging) | Stationary bench |
Emission post treatment | |
Development and characterization of components (catalyst; DeNox: Nox trap, SCR; particulate filter: efficiency, clogging, regenerability study...) | Stationary bench |
Complete vehicule – Roller benches | |
Endurance and reliability (catalyst ageing, particulate filter durability, clutch performance, vehicle/engine/organ validation - cylinder head/injector clogging cycles) | Roller test bench |
Thermal or climatic (Validation tests on alternators in a hot environment on different road cycles) | Roller test bench |
Cold starting, start-up | Roller test bench |
Validation of engine control functions (OBD) on WLTC cycles (and other) | Roller test bench |
Emission or anti-pollution tests (according to standardized cycle) | Emission roller dynanometer |
Stabilized tests (according to standardized cycle) | Emission roller dynanometer |
Performance characterization | Emission roller dynanometer |
Stationary test benches |
Endurance / reliability tests |
- Endurance cycles, |
- Thermal shocks,, |
- Development and execution of fouling cycles. |
Engine architecture characterization tests |
- Measurement of friction losses in drive (cylinder by cylinder with or without combustion), |
- Characterization of function (lubrication circuit, de-oiling, cooling circuit, injectors, EGR (The EGR valve means Exhaust Gas Recirculation. It reduces toxic gas emissions by reusing 5% to 35% of the exhaust gases. ), particle filters, SCR, distribution, turbo ...), |
- Vibratory characterization of the PWT under test, |
- Measurement of instantaneous speeds and characterization of acyclism, |
- Characterization of the lubrication circuit (aeration rate and permeability), |
- Thermal balance. |
Calibration tests of the engine control functions |
Dynamic test benches |
Endurance / reliability tests |
- Simulation of driving on a cycle defined by the customer from vehicle data and the road cycle (speed and gear engaged as a function of time), |
- Testing of sensitive components in transient conditions (air and fuel supply systems, particle filters, etc.) |
Engine architecture characterization tests |
- Measurement of friction losses in drive (cylinder by cylinder with or without combustion), |
- Characterization of functions in dynamics (response time and turbo pumping, lubrication circuit in high transient). |
Calibration tests of engine control functions in dynamics |
- Development of strategies at the reaction of the deceleration input (injector recalibration, maintenance of turbo speed), |
- Simulation of standard cycles (WLTC, FTP-75, 10-15 modes ...), |
- Simulation of engine peripheral components (gearbox ...), |
- Simulation of vehicle operation in hybrid mode. |
Rolling test benches |
Endurance / reliability tests |
- Development and execution of endurance cycles (catalyst ageing, DPF durability, clutch performance, vehicle/engine/organ validation), |
- Cylinder head/injector fouling cycles. |
Climatic tests |
- Validation tests on alternators in a hot environment on different road cycles. |
Functional diagnostic tests |
- Validation of engine control functions (OBD) on WLTC cycles (and others). |
Emission roller test benches |
Anti-pollution tests |
- Realization of antipollution tests according to standardized cycle. |
Stabilized tests |
- Realization of the antipollution tests according to standardized cycle. |
Performance tests |
- Characterization of the performances of a vehicle. |
Depending on whether the vehicles are hybrid, electric or even use a hydrogen fuel cell, different performance topologies are to be considered:
A dynamometer is a device that allows the simultaneous measurement of the torque and rotational speed (rpm or tr/min) of a motor, engine or any other primary rotary engine, in order to calculate its instantaneous power, usually displayed by the dynamometer itself in the form of kW.
By recording a multitude of torque and power values at different speeds, a curve is derived that represents the overall performance of the motor.
In addition to being used to determine torque or power characteristics, dynos are used in standard emissions testing, but also to simulate the road load of the engine or the entire powertrain.
Beyond simple power and torque measurements, dynamometers can be used as part of a test stand for various engine development activities, such as calibration of engine management controllers, detailed combustion behavior studies, etc.
The use of a chassis dynamometer allows to get rid of many parameters influencing full-scale tests (human factor, driving conditions, weather...) and ensures the reproducibility of the tests. It is adapted to validate the consequences of adjustments and modifications.
In most cases, it is necessary to reproduce or simulate all the functions present on the engine in the real application (power steering, alternator, vacuum pump of the braking circuits, air conditioning...).
Thus, for an engine test bench, the engine is associated via a transmission with a load machine (controlled by the engine test bench control) simulating its environment.
The two main operating modes of test benches (braking only or braking and drive) define the two main categories to which they belong: stationary benches and dynamic benches capable of reproducing transients with or without energy generation.
These 2 operating modes correspond to a vehicle, in the acceleration phase (the engine is requested to deliver the power necessary for the vehicle to reach the required speed) and in the braking or engine drive phase (the inertia of the moving vehicle drives the organs and the thermal engine).
Dynamometers have often used eddy current brake type devices as load machines, the control of which imposed a relatively constant resistive torque on the motor under test. These devices are now often replaced by an electric machine which has the advantage of being more dynamic and can supply energy (not just consume it).
During the acquisition measurements, each combination of engine speed (rpm) and torque supplied corresponds to an engine operating point. Given the variations in the dynamic behavior of combustion, hybrid and electric engines according to their operating point, it is necessary to verify the ability of the engine control to ensure the required performance for all operating points of the engine field.
Similarly, it is important that the engine test bed is capable of switching quickly and correctly from one operating point to another. Engine test stands that are capable of fast switching between operating points are called high dynamic engine test stands.
Highly dynamic engine test beds can reproduce vehicle driving phenomena (acceleration, deceleration, gear change, etc.).
.A stationary test bench uses a brake to measure the characteristics of the motor. It is a question of measuring the resistance that the brake opposes to the engine. For a given engine speed, the dynamometer associated with the dyno's braking device can determine the corresponding applied force.
Different technologies of brake dynos exist: eddy current brake, hysteresis brake, powder brake... eddy current brake, hysteresis brake, powder brakes…
The engine to be tested drives a flywheel (an inertia wheel) whose inertial mass is known (calculated - The moment of inertia J=1/2 m*R² - for a full cylinder with m : the mass and R the radius of the flywheel. The energy developed is: E=1/2 J*ώ²).
The more powerful the engine, the higher the speed to time ratio. By making a multitude of measurements of the speed of the flywheel during acceleration we can calculate the torque and power of the motor.
The flywheel is associated with a brake which is used to stop it at the end of the test. It is also used during the engine warm-up phase to prevent the engine from being driven by the flywheel. This brake is not associated with the measurement as is the brake bench.
If there are ways to measure the power, the inertial and the braked. The dynos can often do both knowing that the inertial is the most widespread. Brake dynos have the advantage of being able to simulate an additional load on the vehicle in order to measure the impact of constraints (load, slope etc.).
Emitech Group - Legal information