Laboratories dedicated to mechanical, climatic and physico-chemical environmental simulations
Physical environmental conditions (as opposed to the electromagnetic environment) have always been at the root of qualification testing. The principe is to determine the nature of the environmental conditions that equipment will face, based on its expected usage and life cycle, and to define the key criteria it must meet.
Operating environments are defined by numerous standards, in order to ensure that the phenomena created in laboratory conditions can be reproduced.
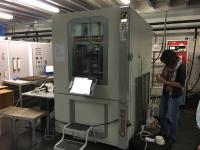
Qualification tests allow us to subject equipment to environmental conditions that are representative of the circumstances in which it will actually be used. These include electromagnetic tests and, in terms of physical environments, climatic tests (resistance to heat, cold, humidity, rapid temperature variations etc.), mechanical tests (vibration, shocks, acceleration), general environmental tests (sand, dust, fungi, solar radiation, salt spray etc.), chemical tests (resistance to fluids, hydraulic pressures), endurance tests etc.
These environmental qualifications can be applied to all sectors of the economy.
They apply to all systems and sub-systems directly exposed to environmental constraints (embedded electronic systems, equipment used outdoors etc.), with specifications determining the severity of these constraints with regard to the relevant levels of stress (satellites, launch equipment, military systems etc.) and the safety requirements of the product in question (control systems, active safety systems etc.).
They also indirectly apply to equipment intended for static, indoor use on account of the stresses to which these materials are subjected during transportation.
A combat helicopter, for example, might be required to take off in a desert (heat), gain altitude rapidly (cold and rapid temperature variation) and then commence automatic weapons firing. This will be reflected in the technical specifications, with thermal constraints (heat, cold, variation) and noise-type variations over a broad spectrum (simulation of exceptional random vibrations - stochastic phenomena - helicopter rotors).
In situ measurements can be used to draft a QTP (Qualification Test Plan).
Standards and specifications (not exhaustive list)
- CEI 60 068-2-x
- ISO 20653
- ...
- B21 7120
- B21 7130
- B25 1140
- B33 2230
- B39 6120
- C00 1000
- D14 1428
- D17 1058
- D45 1234
- D47 1309
- D47 1924
- ...
- 31-05-103
- 31-07-502
- 32-02-027
- 32-02-028
- 32-02-840
- 32-02-048
- 31-00-807
- 34-05-050
- 39-06-211
- ...
- BMW
- CHRYSLER
- DAIMLER-CHRYSLER
- FIAT
- FORD
- GENERAL MOTORS
- JAGUAR
- LAND ROVER
- NISSAN - RENAULT/NISSAN
- PORSCHE
- Cas New Holland
- JOHN DEERE
- IVECO
- MAN
- MERCEDES
- SCANIA
- VOLVO
- ...
- AIRBUS HELICOPTER - NEXTER - PANHARD - ...
- A400M
- FELIN
- VBCI
- LECLERC, CESAR
- PVP
- DASSAULT
- ...
- Altitude (MIL STD 202 method 101E, MIL STD 810 method 500.5, MIL STD 883 method 1001)
- High temperature, low température, temperature cycle (MIL STD 810 method 501.5 et method 502.5, MIL STD 883 method 1001)
- Thermal shock(MIL STD 202 method 107G, MIL STD 810 method 503.5, MIL STD 883 method 1011.9)
- Contamination by fluids (MIL STD 810 method 504.1, MIL STD 883 method 2015.11)
- Solar radiation (sunshine) (MIL STD 810 method 505.5)
- Rain (MIL STD 810 method 506.5)
- Humidity (MIL STD 202 method 103B et method 106G, MIL STD 810 method 507.5)
- Fungus (MIL STD 810 method 508.6, MIL STD 883 method 1004.7)
- Salt fog (MIL STD 810 method 509.5, MIL STD 883 method 1009.8)
- Sand and dust (MIL STD 202 method 110A, MIL STD 810 method 510.5)
- Immersion (MIL STD 202 method 104A, MIL STD 810 method 512.5, MIL STD 883 method 1002)
- Acceleration (MIL STD 810 method 513.6, MIL STD 883 method 2001.2)
- Vibration, fatigue, noise, variable frequency, random frequency (MIL STD 810 method 514.6, method 2005.2, method 2006.1, method 2007.2, method 2026)
- Acoustic noise (MIL STD 810 method 515.6)
- Mechanical shocks (MIL STD 810 method 516.6, MIL STD 883 method 2002.3)
- Pyroshock (MIL STD 810 method 517.1)
- Gunfire shocks (MIL STD 810 method 519.6)
- Temperature, humidity, vibrations and altitude (MIL STD 810 method 520.3)
- Icing and freezing rain (MIL STD 810 method 521.3)
- Vibro-acoustic and temperature (MIL STD 810 method 523.3)
- Mechanical vibration of shupboard equipment (MIL STD 810 method 528)
- Flammability (MIL STD 202 method 111A)
- ...
- NATO - STANAG 4370
- NATO - STANAG 2895
- ...
- GAM EG 13
- DEF STAN 00-35
- ...
- AIRBUS
- BOEING
- BOMBARDIER
- DASSAULT
- AIRBUS HELICOPTER
- DASSAULT
- ARIANE
- ...
The RTCA DO-160G "Environmental Conditions and Test Procedures for Airborne Equipment" document sets out to define a series of test environments and procedures for on-board equipment in aircraft. The environments and procedures applied to an equipment item depend on the category defined in these documents, according to the type of aircraft, its conditions of use and how the equipment is installed in the aircraft.
This document is also referenced under the name EUROCAE ED-14G.
Mechanical, climatic and physical-chemical environments
- Airbus: ABD0100.1.2
- Airbus: ABD0100.1.8.1
- Boeing: 787B3-0147
- Altitude (MIL STD 202 method 101E, MIL STD 810 method 500.5, MIL STD 883 method 1001)
- High temperature, low température, temperature cycle (MIL STD 810 method 501.5 et method 502.5, MIL STD 883 method 1001)
- Thermal shock(MIL STD 202 method 107G, MIL STD 810 method 503.5, MIL STD 883 method 1011.9)
- Contamination by fluids (MIL STD 810 method 504.1, MIL STD 883 method 2015.11)
- Solar radiation (sunshine) (MIL STD 810 method 505.5)
- Rain (MIL STD 810 method 506.5)
- Humidity (MIL STD 202 method 103B et method 106G, MIL STD 810 method 507.5)
- Fungus (MIL STD 810 method 508.6, MIL STD 883 method 1004.7)
- Salt fog (MIL STD 810 method 509.5, MIL STD 883 method 1009.8)
- Sand and dust (MIL STD 202 method 110A, MIL STD 810 method 510.5)
- Immersion (MIL STD 202 method 104A, MIL STD 810 method 512.5, MIL STD 883 method 1002)
- Acceleration (MIL STD 810 method 513.6, MIL STD 883 method 2001.2)
- Vibration, fatigue, noise, variable frequency, random frequency (MIL STD 810 method 514.6, method 2005.2, method 2006.1, method 2007.2, method 2026)
- Acoustic noise (MIL STD 810 method 515.6)
- Mechanical shocks (MIL STD 810 method 516.6, MIL STD 883 method 2002.3)
- Pyroshock (MIL STD 810 method 517.1)
- Gunfire shocks (MIL STD 810 method 519.6)
- Temperature, humidity, vibrations and altitude (MIL STD 810 method 520.3)
- Icing and freezing rain (MIL STD 810 method 521.3)
- Vibro-acoustic and temperature (MIL STD 810 method 523.3)
- Mechanical vibration of shupboard equipment (MIL STD 810 method 528)
- Flammability (MIL STD 202 method 111A)
- ...
- NATO - STANAG 4370
- NATO - STANAG 2895
- ...
- GAM EG 13
- DEF STAN 00-35
- ...
Instrumentation implemented
- Number: 8
- Usable volume: 0.4 to 13 m3
- Automated cycles (salt spray, drying, moist heat)
- Number: 6
- Temperature: -70 to +190 °C
- Transfert time: under 10 s
- Software control
- Usefull dimension (mm): 790 x 740 x 850
- Number: 60
- Usefull volume: from 0,1 to 93m3
- Temperature range: -70 to +650 °C
- Rapid temperature variations: 20 °C/min
- Humididy: from 10 to 100 % Hr
- Number: 6
- Temperature range: -70 to +150 °C
- Rapid temperature variations: 20 °C/min
- Humididy: from 20 to 100 % Hr
- Software control, remote alarms
- Usefull dimension (mm): 1200 x 1200 x 1200
- Number: 35
- Frequency: 3 to 3000 Hz
- Force: 7 to 105 kN
- Displacement: 300 mm
- Table simensions (mm): 1500 x 1500
- Number: 12
- Frequency: 0 to 300 Hz
- Force: 200 kN
- Displacement: 300 mm
- Table simensions (mm): 3000 x 3000
- Number: 2
- Frequency: 2 kHz à 50 kHz
- Force: 250 kN
- Max. acceleration: 100g
- Force: 5 000 N
- Frequency: 0.1 - 50 Hz,
- Max. acceleration: 30 gn
- Max. speed: 6.0 m/s
- Displacement: 350 mm peak-to-peak
- Max. mass: 50 kg
- Associated horizontal table, adjustable from 400 mm to 600 mm
- Number: 4
- Max. acceleration: 400 g
- Max. diameter: 3000 mm
- Number: 8
- Max mass: 1 t
- Table simensions (mm): 800 x 800
- Number: 2
- Altitude testing from 5000 feet to 100,000 feet (10 mBar).
- Overpressure tests can be carried out up to 1 relative bar or 2 absolute bar.
- Fast decompression tests can be performed in less than 7s (560 l enclosure)
- 100 mbarA in less than 2 seconds on a volume of 100 litres
- Number: 1
- Usefull dimension (mm): 1m3
- Wind: adjustable speed from 2.4 to 25 m/s (on a 1m² section)
- Humidity: regulated to be less than 30% Hr
- Temperature: 23°C to 70°C
- Concentration sand and dust: 0 and 10 g/m3.
- Frequency: 0.1 to 100 Hz
- 16 acquisition channels
- Sinus control, random, shock (S. R. C.) in bi-axis
"Together" configuration
- Force: 50kN horizontal and 2*30kN vertical
- Displacement: max. 250 mm peak-to-peak horizontal and 100 mm peak-to-peak vertical.
- Max. mass: 900 kg
- Table: 1100 * 1200mm
"Component" configuration
- Force: 50kN horizontal and vertical
- Displacement: max. 250 mm peak-to-peak horizontal and vertical
- Max. mass:100 kg
- Table: 450 * 450mm
Measurement and data acquisition
- Capacitive accelerometer sensors, charge, ICP,...
- Wireless displacement sensors, LVDT,...
- Strain gauges
- …
- Fluid contamination
- Sun exposure
- Solar rays
- Cooling, Icing
- Fire testing
- Pyrotechnic shocks
- Mould and fungus control
- Static mechanical testing up to 1500kN
- Voltage
- Current
- Rotation speed
- Micro power cuts
- Thermal imaging
- Laser Doppler Vibrometer
- Warping and physical pressures
- ...
Liquids
- 6 oil systems: 1 to 75 l/min, 10 to 250 bar, -20 to 130°C
- 4 glycol benches: 8 to 14 m3/h, 3 bar, -40°C à +135°C
- 2 Skydrol units: 1 to 9 l/min, 450 bar
- 4 injection systems: 10 to 525 bar
- Auxiliary equipment: 50 kW oil heater, 700 bar hand pumps...
Air
- 1 pressure / decompression test bench: 0,1 to 2 barA
- 5 pressure / decompression chambers
- 3 air heaters 200 to 300°C – 1 x 650 kW fuel burner
- 5 x 650°C air heaters, 600°C heat chamber, 454°C / 60 bar valves ...
- Cyclic pressure
- Cyclic flow
- Cyclic temperature
- Circulation at controlled temperatures
- Burst resistance pressure
- Stress tests
- Pulse testing
- Power loss
- Leaks
- Rotary flexure
- Combined temperature, vibration and pressure tests
- All types of specialist testing on request
- Volume: 1140 dm3
- Temperature: -100 à +200 °C
- Rapid temperature variation: up to 60°C/min
- Vibrations:
- random and omni-axial
- frequency range 10 to 10000 Hz
- maximum acceleration: 60 gRMS
Meeting the very latest reliability requirements.
At the design stage, maximise the robustness of your products by exploring the limits of their functionality and structural integrity.
In the manufacturing phase, eliminate underlying faults and optimise your fabrication processes and supply chains.